Steel Railway Parts Produced by Casting: Benefits and Applications
Steel railway parts produced by casting are essential components of the railway system. These parts are used in the construction of railways and are responsible for ensuring the safety and efficiency of the system. Cast steel is a popular material for railway parts due to its strength, durability, and resistance to wear and tear.
The process of casting steel railway parts involves pouring molten steel into a mold to create the desired shape. This method is preferred over other manufacturing techniques because it allows for the creation of complex shapes and designs. Additionally, casting allows for the production of large quantities of parts at a lower cost. Cast steel railway parts are used in various applications, including rails, sleepers, and switches.
Production Process
Casting Process
Steel railway parts are typically produced using a casting process. This involves melting down steel and pouring it into a mold to create the desired shape. The mold is usually made of sand or a ceramic material, and is designed to withstand the high temperatures and pressures involved in the casting process.
Once the steel has been poured into the mold, it is left to cool and solidify. This can take several hours, depending on the size and complexity of the part. Once the part has cooled, it is removed from the mold and any excess material is trimmed away.
Heat Treatment Process
After the casting process is complete, the steel railway parts are typically subjected to a heat treatment process. This involves heating the parts to a high temperature and then cooling them rapidly. This process is designed to improve the strength and durability of the parts, making them better suited for use in railway applications.
During the heat treatment process, the steel is heated to a temperature of around 900-1000 degrees Celsius. It is then cooled rapidly using water or oil, which causes the steel to harden and become stronger. This process can also help to remove any residual stresses in the steel, which can improve its overall performance.
Overall, the production process for steel railway parts involves a combination of casting and heat treatment processes. These processes are designed to create parts that are strong, durable, and well-suited for use in railway applications.
Quality Control
Quality control is an essential step in the production of steel railway parts. Casting is a complex process, and there are many factors that can affect the quality of the final product. To ensure that the parts meet the required specifications, a rigorous quality control process is necessary.
Non-Destructive Testing
Non-destructive testing (NDT) is a critical part of the quality control process. It involves the use of various techniques to inspect the parts without damaging them. NDT can detect surface and subsurface defects, such as cracks, porosity, and inclusions, that can affect the performance of the parts.
There are several NDT methods that can be used, including:
- Ultrasonic testing: Uses high-frequency sound waves to detect defects.
- X-ray testing: Uses X-rays to create images of the parts.
- Magnetic particle testing: Uses magnetic fields and iron particles to detect defects.
- Liquid penetrant testing: Uses a liquid dye to detect surface defects.
NDT is an effective way to ensure that the parts meet the required quality standards. It helps identify any defects early on in the production process, allowing for corrective action to be taken before the parts are shipped to the customer.
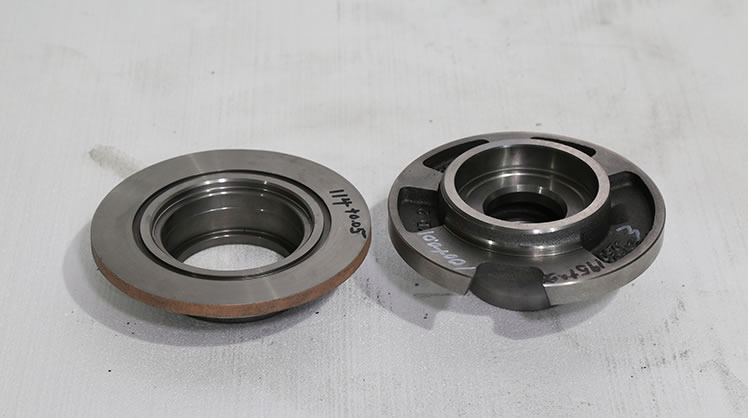
Dimensional Inspection
Dimensional inspection is another crucial part of the quality control process. It involves checking the dimensions of the parts to ensure that they meet the required specifications. This is important because even small variations in dimensions can affect the performance of the parts.
There are several methods that can be used for dimensional inspection, including:
- Coordinate measuring machines (CMMs): Use a probe to measure the dimensions of the parts.
- Optical measuring systems: Use cameras and software to measure the dimensions of the parts.
- Gauge blocks: Use a set of precision blocks to check the dimensions of the parts.
Dimensional inspection is essential to ensure that the parts are within the required tolerances. It helps prevent issues such as improper fit, which can lead to safety concerns and increased maintenance costs.
In conclusion, quality control is a critical part of the production of steel railway parts. NDT and dimensional inspection are two key methods used to ensure that the parts meet the required quality standards. By using these methods, manufacturers can produce high-quality parts that meet the needs of their customers.
Advantages of Steel Railway Parts Produced by Casting
Durability and Strength
Steel railway parts produced by casting offer a range of advantages over other materials. One of the key benefits is their durability and strength. Steel is a robust and sturdy material that can withstand heavy loads and harsh weather conditions. This makes it ideal for use in railway parts, which must be able to withstand the wear and tear of constant use.
Casting is a process that allows steel to be shaped into complex forms, which further enhances its strength and durability. Complex shapes can be produced with ease, which means that railway parts can be designed to meet specific requirements. This makes it possible to produce parts that are stronger and more durable than those made from other materials.
Cost-Effectiveness
Another advantage of steel railway parts produced by casting is their cost-effectiveness. Steel is a relatively inexpensive material, which means that it is an affordable option for railway parts. Casting also allows for the production of large quantities of parts at a relatively low cost.
In addition, steel railway parts require less maintenance than parts made from other materials. This is because steel is resistant to corrosion and wear, which means that it can last for many years without needing to be replaced. This reduces the overall cost of maintaining the railway system and ensures that it remains operational for longer periods of time.
Overall, steel railway parts produced by casting offer a range of advantages over other materials. They are durable, strong, and cost-effective, making them an ideal choice for use in railway systems.
Applications
Railway Tracks
Steel railway parts produced by casting are commonly used in the manufacturing of railway tracks. These parts include rail chairs, rail braces, and rail joints. Rail chairs are used to secure the rails to the sleepers, while rail braces are used to hold the rails in place and maintain their position. Rail joints are used to connect two sections of rail together.
Casting is an ideal process for producing these parts because it allows for complex shapes to be created with high precision. The resulting parts are durable and able to withstand the wear and tear of heavy trains passing over them. Additionally, steel railway parts produced by casting are resistant to corrosion and can last for decades with minimal maintenance.
Railway Bridges
Steel railway parts produced by casting are also used in the construction of railway bridges. These parts include bridge bearings, bridge girders, and bridge plates. Bridge bearings are used to transfer the weight of the bridge to the supporting structure, while bridge girders provide support for the bridge deck. Bridge plates are used to secure the bridge girders to the supporting structure.
Casting is an ideal process for producing these parts because it allows for large, complex shapes to be created with high precision. The resulting parts are strong and able to withstand the weight of heavy trains passing over them. Additionally, steel railway parts produced by casting are resistant to corrosion and can last for decades with minimal maintenance.
Overall, steel railway parts produced by casting are an essential component of the railway industry. They provide the strength and durability needed to support heavy trains and ensure safe and reliable transportation.
Our railway castings are mainly for rail rolling stock and railway infrastructure. Typical railway castings are:
- Axle boxes
- Alex bod housing
- Centre plates
- Bearing bracket
- Pedestals
- Door hinges
- Yokes
- And more
We make precision railway castings in any cast alloys as required including cast stainless steel, and have the expertise and ability to work with you on design also combing the application of components. we take pride in the quality and service of casting components for our clients. Each railway casting from our company must pass through the strict quality control system both during and after production. This ensures us to produce railway castings workable in the toughest conditions.
Whatever the railway castings you need, pls contact our investment casting foundry, we are able to assist you to find a lasting solution for your project. Just pls get in touch first! We are committed to supplying competitive prices based on high quality railway castings.